Reliability, Availability, and Maintainability (RAM) analysis is a vital approach to ensure the seamless operation of any system throughout its lifecycle. By assessing potential vulnerabilities in system design, maintenance strategies, and operational processes, RAM analysis plays a key role in minimizing downtime, optimizing performance, and meeting project objectives.
The process identifies factors that could reduce operational availability or limit production efficiency. Once pinpointed, these insights drive improvements to system design and maintenance practices, ensuring that project goals and performance standards are achieved.
Addressing Key Areas of Focus
- Balancing Design and Cost:
Systems must perform reliably without exceeding budget constraints. Striking this balance requires data-driven decisions to ensure cost-effective solutions without compromising operational standards. - Streamlining Maintenance Plans:
Effective maintenance strategies are the backbone of system reliability, but developing these plans can be resource-intensive. A structured approach reduces complexity and creates efficient workflows that support long-term performance. - Forecasting Availability and Capacity:
Reliable operations hinge on accurate predictions of equipment availability and capacity. Informed planning ensures optimal resource allocation and eliminates unexpected disruptions.
The Lifecycle of RAM Analysis
From early conceptual design to detailed execution, RAM analysis evolves alongside a project. During initial phases, high-level assumptions guide the process, which matures into precise failure-mode modeling as the project progresses. This dynamic approach integrates seamlessly into project development, ensuring alignment with operational goals.
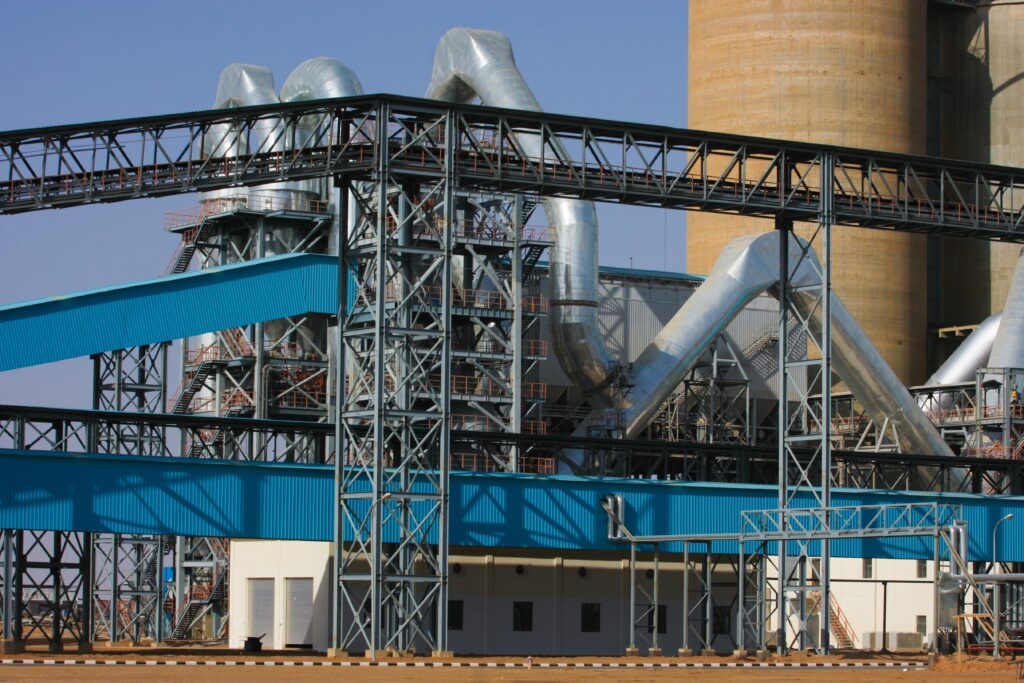
What RAM Analysis Delivers
- Early Design Validation:
By analyzing equipment interdependencies and potential failure points, early-stage RAM analysis helps refine design choices. Tools like Reliability Block Diagrams (RBDs) highlight critical areas, enabling proactive improvements. - Data-Driven Maintenance Strategies:
As systems are developed, RAM analysis establishes a reliable foundation for maintenance planning. Key data such as failure rates, redundancy needs, and spares availability are documented, creating actionable insights for operational teams. - Optimized Spare Parts Management:
Efficient spare parts management minimizes the cost of holding excess inventory while ensuring timely availability during both planned and unplanned maintenance activities. - Informed Decision-Making:
Whether determining refurbishment needs or planning preventive maintenance, RAM analysis empowers teams with the clarity to make confident, cost-effective choices that align with operational priorities. - Comprehensive System Modeling:
A detailed system model incorporates every project aspect, from equipment specifications to maintenance workflows. This ensures alignment across procurement, vendor collaboration, and resource allocation, reducing redundancy and enabling smooth ramp-up phases. - Capacity and Availability Insights:
RAM analysis evaluates all system variables—utility dependencies, redundancy configurations, material transport processes, and regulatory compliance. This holistic view identifies bottlenecks and ensures that the system operates at peak capacity. - Seamless Integration with Maintenance Systems:
Standardizing maintenance strategies across an organization reduces inconsistencies and creates a unified approach. By integrating RAM insights into Enterprise Asset Management (EAM) systems, teams ensure efficiency from strategy development to execution.
Building Long-Term Success
RAM analysis is not a one-time activity; it is an integral part of a project’s evolution. By incorporating it at every stage, organizations can achieve greater reliability, minimize disruptions, and create systems designed for both present and future demands.